Sydney has a new resident. M/Y Bluestone 1 is 101 feet of sophistication and fun and already turning headings in Australia’s busiest harbour.
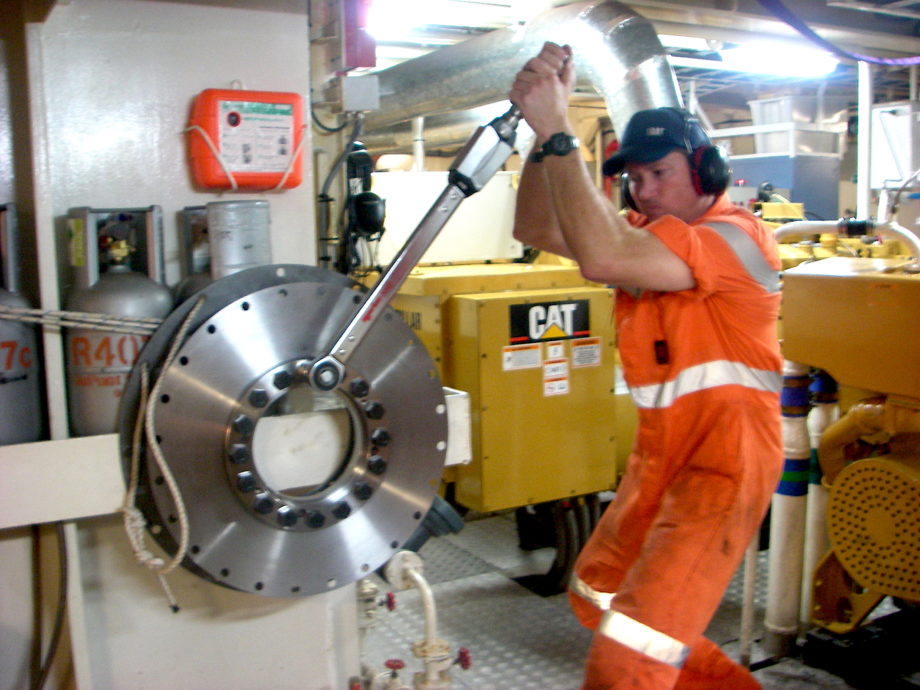
We caught up with DCV Marine’s Rhett Sullivan to talk planned maintenance software and how his ongoing work as an AMSA Accredited Surveyor has been affected by the introduction of digital software.
Tell us a little about yourself and what your role is at DCV Marine as an AMSA accredited surveyor?
I am a marine diesel fitter by trade, AMSA Engineer class 3, Y2 and AMSA Accredited surveyor with 27 years marine industry experience. During this time frame I have worked commercially, offshore oil and gas and international superyachts accumulating 4500 days sea time, many refits and a new build. I live in Coffs Harbour NSW Australia.
DCV Marine was set up as a Marine surveying, consulting, engineering and project management company. Within this structure I have been surveying Australian domestic commercial vessels, private and insurance surveys and expert witness. Relief engineer on yachts. Set up full implementation of planned maintenance programs on yachts. Teaching marine engineering. Project managing yacht refits.
From an AMSA Accredited surveyor perspective, how important do you see an implemented PMS onboard? Are digital solutions your preference?
If a vessel is well maintained, it will pass survey easier. If a vessel is operating at a level that it will pass survey and / or Port state inspections at any given time it will be a safer highly functional vessel. A well implemented PMS will deliver this positive outcome. A survey shouldn’t be something that crew start getting ready for a week in advance, good crew should almost treat surveys as a personal competition, ‘Go ahead, try and find something wrong with my boat’.
A well implemented PMS can minimise the human factor, crew aren’t just doing what they want to do when they want to do it. They are conforming to a system that has been developed specifically for that vessel based on a range of factors such as; Equipment manufacturers recommendations, industry standards, operational requirements and statutory regulations.
Digital planned maintenance solutions are preferable for a range of reasons such as –
A lot of questions can get asked during survey. I find it most beneficial when I can work in with the marine crew and get answers quickly from a central system such as Seahub that has the parts on board listed or how we go about servicing critical equipment and proof of how often it is done etc.
Digital systems are time stamped, so crew cannot update information after the fact.
Whilst going through certain records, history, planned maintenance it is easy to extract PDF files as a print out or email as proof for the surveyors records.
When a crew member really knows there way around the digital PMS then they generally know there way around the vessels critical equipment also, this makes the survey go smoother.
New crew who may not know the vessel as well can gain access to a lot of data.
What benefits do digital solutions bring compared to paper based maintenance records?
Digital PMS are quicker to get around and don’t require understanding peoples hand writing or delving into folders and filing cabinets.
They are backed up ashore and can be accessed remotely.
Rotational crew can access the PMS remotely before crew change day and be very familiar with their expectations on crew change day.
New crew and relief crew in officers roles can get up to speed with the vessel they are joining before arrival.
This generation of marine crew are all using technology to a high level. An electronic PMS is just a natural extension of this process that will only get more and more complex into the future.
Digital solutions allow for large data retention which can be very useful for a range of reasons too numerous to mention.
When conducting a survey onboard a vessel, what value does a PMS bring to you as an AMSA Accredited Surveyor and your findings when looking to understand the history or condition of equipment onboard?
Often the questions are asked, ‘How often do you service / check / inspect a certain piece of equipment’. A surveyor is looking for and must receive proof that the answer provided was actually done.
If say the chief engineer is asked what maintenance is done to the steering gear. Then he can provide the planned maintenance list, then some itemised unplanned jobs, then a history of what was done and when, using what parts. And then prove the parts that are carried aboard and when they are used and updated then we see a trend of proof of work done. This of course can be retained electronically or printed out if required by the surveyor.
This can happen in short time frame making the time spent aboard more efficient.
You have used Seahub on a regular basis. What other tools in Seahub besides maintenance, do you see as useful for a vessel, including those that are AMSA classed?
Equipment: The List of machinery is the basis for maintaining a vessel. Capturing the make, model, serial no. etc is very useful and can save a lot of time when maintaining and parts ordering.
Inventory: A must have item, ask any engineer. You often can’t fix it if you haven’t got the parts. When a breakdown is being dealt with, quickly knowing the part you need is on board in a specific location is a must.
Warranty: Great to have on newer vessels I have seen a lot of money get wasted with new vessels or equipment missing its warranty period.
Fluid analysis: As a diesel fitter, surveyor and engineer I cannot speak highly enough of the $40 oil analysis and its worth. A quick process that delivers so much benefit for its small price. A great way of getting to know what’s happening inside your engines, gear boxes, hydraulics etc. When these are linked and captured in Seahub they become and even more useful to the engineer and easy proof for the surveyor. Also, another way of reducing the inefficiencies of dealing with hard / paper copies.
Projects: Yachts do projects all the time and some of them may not be managed that well. A great tool to link the worklists and better organise for refits. Also, beneficial as it can be viewed shore crew.
Documents: Very beneficial to have all manuals, drawings, certificates etc electronically stored and linked to components. Greatly assists in hard copies not being lost. Good place to mange ISM Compliance.
For more information on DCV Marine and locating an AMSA Accredited Surveyor visit their website today:
For more information on Seahub just visit us here: