The team at Seahub – Yacht Maintenance Software are thrilled to announce the launch of a new technology aimed at effectively managing new build & commissioning worklists.
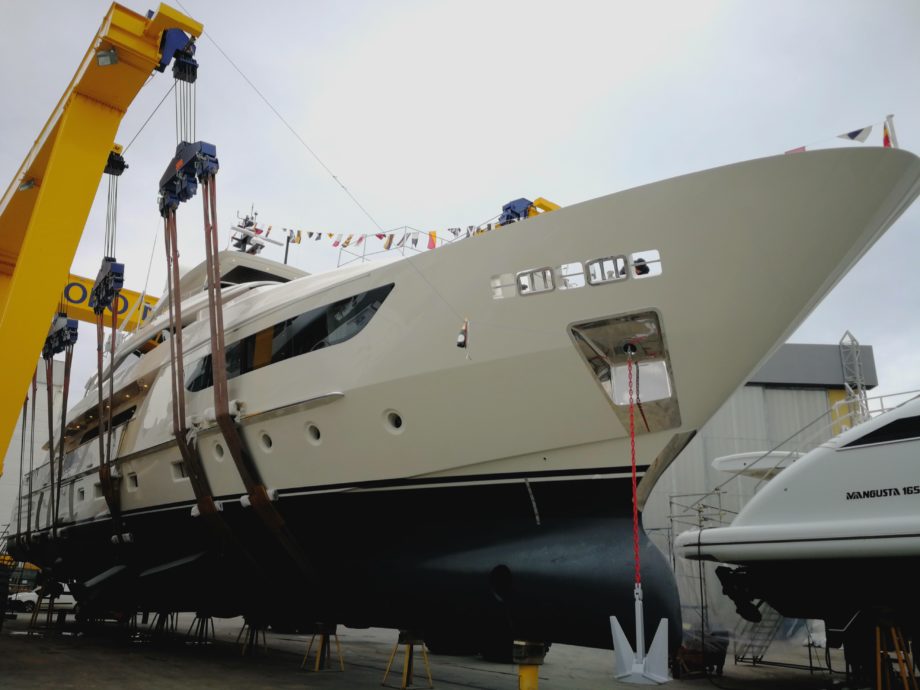
New Build, M/Y Sosa is full steam ahead into a busy Mediterranean season after successfully launching in late April this year from the San Lorenzo yard in Italy. After an extensive build phase Chief Engineer Edward Robertson finally had some time to breathe and bring us in to implement a planned maintenance system tailored to their build. After spending time onboard in late May with the M/Y Sosa crew, we caught up with Edward to see how Seahub is working out for him.
As the Chief Engineer of a new build, how was the decision made to implement a planned maintenance system from when the vessel was newly launched?
We wanted a user-friendly system that would provide myself and crew to have a daily maintenance plan to work from, and a system that we can keep track of inventory, file documents digitally and log all our maintenance for future reference and fault finding etc.
When comparing solutions on the market, what were the key reasons for choosing Seahub?
I chose Seahub because the fact it requires no special software, it can be used on any device onboard, its secure and backed up offsite, and because of its fully featured easy to use interface.
Seahub completed an onsite account set up and data entry as part of the deployment. How did you find the collaboration between yourself and the Seahub team during the setup process and what were the end results?
This was well worth having Seahub onboard to compile our system. It worked seamlessly even though we had a surprise guest trip in the middle of it.
As a result, our system was setup with as much detail as possible while being tailored to how I wanted it to work.
Even though Seahub is very easy to use, having the team onboard we were able to go over some finer details and learn how to get the most out of it.
Now that you are using Seahub, what functionality are you finding the most value in?
I find the most value in not having to plan and record maintenance which saves on time, office space and the complexity of working schedules manually. I check Seahub and its laid out what I need to do that day and what’s coming up in the future.
I’m also starting to plan a shipyard period with Seahubs Project feature, this will be a valuable reference in winter.
The experience of having a Seahub representative on board during the new build phase and hands on during the account set up often plays a big role in bringing the users of the system up to speed quicker while also providing a chance for the sharing of set up approaches which often result in smoother long-term results. Technical Director Matt Hyde, worked very closely with Edward during every phase of the account setup.
“Edward and San Lorenzo were great partners in this project. He was willing to give up his time and work together on ensuring the database was customised to his needs. All in all, the project was an enormous success. Thanks to the whole crew on Sosa for having us onboard!” says Hyde.
To hear more success stories of Seahub implementations onboard superyachts, please get in contact with the team today!